Wednesday, April 26, 2006
Maker Faire 2006
This past weekend I went to Maker Faire. There was lots of neat stuff
on display, including a firetruck that belched flames at random
intervals, a life-size robotic giraffe (life size for a giraffe, that
is), and games of Segway Polo.
There were also a number of workshops and presentations. For many of
the workshops you were supposed to sign up in advance, but in many cases
it was possible to get in without doing this. In the worst case you
could still observe workshops even when it wasn't possible to get into
them.
The first presentation I went to on Saturday was
Control Lights and Appliances using Express Tools. This was
a thinly veiled ad for Microsoft's Visual Studio Express Tools. The
presenters were trying to show how one could control lights via X10
using C#, but their x10 modules kept flaking out. The presenters were
university students (one from Stanford and one from Berkeley), and a
sales guy from Microsoft who seemed like he would've been more at home
coaching a football team. Overall, the presentation was at the wrong
level for the audience. As far as I could tell, most, if not all, of the
people in the audience were proficient programmers, yet the Microsoft
guy kept prompting the two students to explain basic programming
concepts like "what is a comment".
Things went uphill from there. The next thing I checked out was a
workshop by Perry Kaye from Think Solve Do!, Inc. I think this was $200
Machine Shop. I wasn't actually in the workshop (I got there too late,
and I hadn't signed up), but watching it was pretty interesting. Perry
demonstrated a number of interesting techniques for building "prototypes"
of inventions very quickly and at low cost. For example, he suggested
drawing 2D designs on a computer, printing them out at 1:1 scale, gluing
the printout to a sheet of wood, and then using a scrollsaw. He also
talked about epoxy putty, and a technique for making molds and casting
parts in Alumilite resin.
After this I went to a talk on Hacking USB Keyboards. The basic idea was simple: get a (cheap) USB keyboard, open it up and label the key contacts, follow the traces back from the contacts for the keys you care about, and finally connect your own switches or sensors to the lines. Using this technique one could connect a large number of binary (ie: on/off) sensors to a PC.
I then went to a talk by Bruce Shapiro called The Art of Motion Control.
Bruce had a number of neat things on display including "ribbondancer", a
tower that gracefully swings a pole with a ribbon at the end
continuously, all day long; "Eggbot", a shoebox sized device
that can draw intricate designs on eggs or lightbulbs; and a computer
controlled Etch-A-Sketch. Many of Bruce's devices would be called
"robots" to many people, but he prefers the term "motion control". I
think this may be to avoid getting people's hopes up. His devices look
nothing like humanoids: they're very special purpose machines for
creating (or being) art.
In his talk Bruce explained how he gave up his career as a medical
doctor to become an artist and educator, and described a number of other
projects that he's worked on.
The last presentation I went to on Saturday was Precision
Woodworking / Puzzles by Lee Krasnow. Lee explained
his process for creating extremely precise 3D wooden puzzles. A
lot of these are platonic solids or starred platonic solids which
disassemble/reassemble only if you know the right sequence of moves.
Despite the fact that he's working with one of the oldest materials
known to man (wood), Lee uses some very modern techniques to
get the precision that he demands. He uses a computer controlled saw and
a series of jigs that he built himself for cutting everything. He
doesn't sand anything (sanding is imprecise, after all). Instead, he
cuts very slowly, and he has the saw programmed to slow down
even more at the end of the cut. He also always cuts with the grain
rather than against it. Pieces where the cut was against the grain he
refinishes by running them through the saw a second time facing in the
opposite direction.
For fastening the pieces together he uses pins, not glue. Because many of the pieces are strange shapes that are hard to work with he has a bunch of jigs that he designed in 3D CAD and then had 3D printed.
By the end of the day I thought I'd seem just about all of the booths. I was surprised that I hadn't really seen much Lego, since I'd heard that Lego was a sponsor. I looked at my map and realized that I'd missed one area.

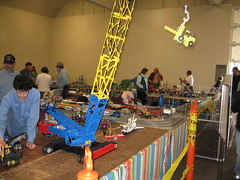
"Maker Hall B" had huge displays of Lego including an enormous (probably about 400 square feet) Lego City with numerous working trains, a massive Lego crane (more than 15 feet tall, I'd guess) and many other Lego creations like a "Lucky Cat".
The new NXT Mindstorms sets were also
on display. I was surprised at how small some of the new pieces (like
the sonar sensor). I'd only ever seen them in photos, and so I didn't
have a proper sense of scale.
The next day I went to a talk on Instructables by Eric Wilhelm.
Instructables is sort of like Flickr for tutorials. One thing I found
really interesting was the way that they'd thought about the issues of
refactoring and re-use. Just as you factor common operations in a
computer program out into reusable functions/classes/whatever, in
Instructables it's useful to be able to factor out part of one tutorial
(eg: the part on "how to use a hammer") for use in another tutorial.
Next, I went to a talk on Processing. Processing is a somewhat goofy little scripting language, but it's quite good at one thing: making it really easy to create artwork and animation from code. The tutorial reminded me of when I used to write programs on my Commodore 128 in BASIC 7.0 for drawing fractals and geometric art. It made me want to dig up those old programs and recode them in processing.
I then went to the only workshop I'd actually signed up for in advance, Build Your Own RFID Reader presented by Parallax. For $15 we were given about $100 worth of Parallax products including an RFID reader, a Basic Stamp 2 "HomeWork" board, two RFID tags and a bunch of software and documentation in a addition to being told how to use it. We have two cats, and the bigger one is always eating the smaller one's food. My plan is to put an RFID tag on him, and then rig up something around the other cat's bowl that will scare him away if he tries to steal food.
I also went to a presentation called DIY Touchpanels given by Sasha Harris-Cronin. She talked about a bunch of different techniques for building touchpanels including computer vision, RF, capacitance, and a bunch of others. It was pretty interesting as she showed a bunch of examples and explained the pros and cons of each implementation.
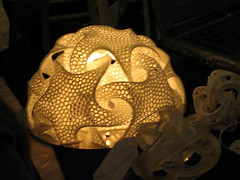

One of my favorite exhibits at the Faire was the 3D artwork by Bathsheba Grossman. Some of it she designs using 3D modeling software, and some she creates with software she writes herself. She then uses 3D printing to produce the most amazingly intricate paperweights I've ever seen.

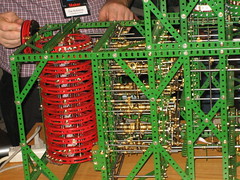
Here's a little video I made of Tim and his difference engine: